ECTA Safety Committee/Safety Recommendations for Palletisers
Download recommendation as PDF
Preliminary remarks:
In the tube and core industry, equipment used to manufacture and package tubes and laminated paper cores differs in size and type, depending on the manufacturer. The ECTA Safety Committee has made an effort to take into account all existing differences in writing these safety recommendations. Therefore, the tube packaging and palletising equipment shown here are to be seen as examples. Custom-made equipment designed for adjusted packaging can sometimes differ considerably from the model shown.
The committee advises you to take national standards and norms into account when applying ECTA safety recommendations. The current Machinery Directive 2006/42/EC and the relevant CE norms are to be observed as well. When in doubt, coordinating with local safety authorities is recommended!
A. Basic requirements
I. Documented risk analysis
II. At least one (1) written documented safety seminar per year for all employees who work with the equipment led by the direct supervisor together with an industrial safety expert
III. The emergency stop chain of the packaging equipment is an integrated component of the entire emergency stop chain of the preceding and subsequent transport equipment (hoisting devices and grippers or robotic equipment to aid feeding).
IV. All areas which do not need urgent access should be secured with a solid enclosure to prevent unintentional entrance.
V. All areas which need to be accessible, especially the area where new pallets are brought or where full pallets are removed, must be secured with light curtains.
VI. During the removal of full pallets or feeding new pallets, the packaging process must be interrupted.
VII. Any protective devices which already exist on the equipment may not be removed or taken out of service.
VIII. Placement of visual warnings at dangerous spots which cannot be secured due to the nature of the operation, such as near machine’s tube feed area.
B. Basic elements of the technical safety devices
I. Direct protection of moving parts.
1. Protective cover over access areas with contact switch which is closed on all sides.
2. Emergency stop mechanism
2.1 Emergency stop button
2.2 Access doors with contact switches
II. Area safeguarding during normal operations
If necessary, additional safety devices on the input and output openings, not necessary if fully encased.
III. Area safeguarding during setup operations
1. Central switch toggling between set-up mode and normal operation
2. Automatic step-by-step control during set-up mode (every step of a cycle has to be activated by hand)
3. When in set-up mode, hardware safety features need to be secured.
An example for packaging / palletising equipment for cores and tubes from 1 to 10m in length is enclosed as an Appendix.
Remarks:
If the machine is substantially altered, the original CE certificate issued by the manufacturer lapses and the user has to have a new one issued in a timely manner.
Approval of the safety concept by institutions responsible for such inspections at the national level is highly recommended.
Waiver of liability:
ECTA has made an effort to draft these safety recommendations in good faith using the knowledge available to it. The recommendations are non-binding. Guarantee claims cannot result from following them. The recommendations do not release members from informing themselves of the current legal statutes and of their individual application needs.
Appendix: Schematic depiction of palletising equipment safety features
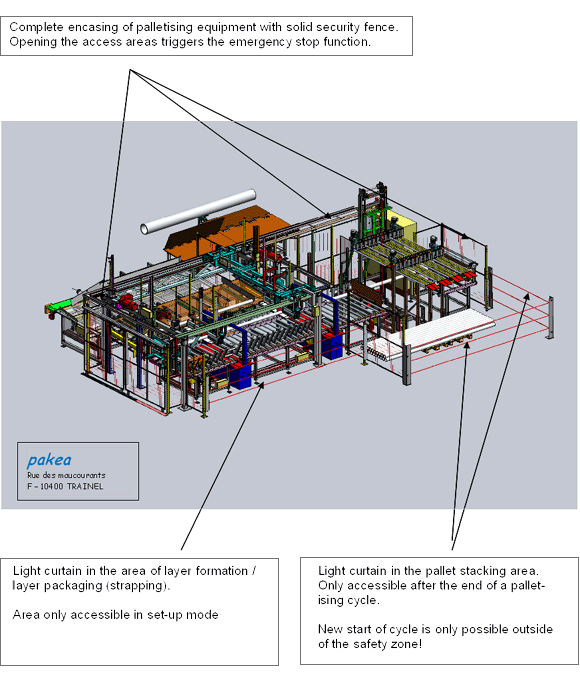
Figure 1: Schematic depiction of palletisers safety features
large version of image